2019年10月21-24日,2019北京国际风能大会暨展览会(
CWP2019)在北京隆重召开,大会主题“风电助力‘十四五’能源高质量发展:绿色、低碳、可持续”。自2008年首次在北京举办以来,已连续举办11届,成为北京金秋十月国内外风电行业争相参与的年度盛会。
10月24日,风电机组技改专题论坛在新国展召开。浙江
运达风电股份有限公司主任工程师/博士
杨波出席论坛并发表演讲。
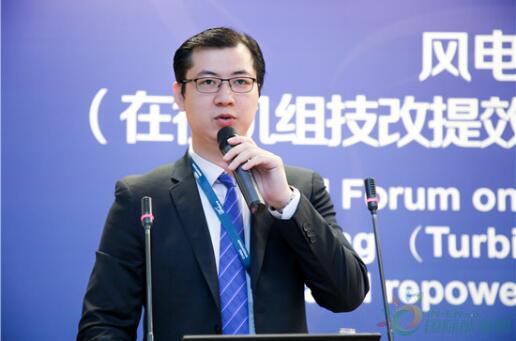
以下为发言内容:
杨波:各位来宾各位专家,我是来自运达股份的杨波,今天很高兴在这个平台和大家分享一下我们运达在役叶片损伤检测。分成四个题目,分别是背景概述、运维的现状、还有我们运达的一个方案,最后是我们实验的一个结果。
我们知道到2018年全国累计装机量2.1亿千瓦,连续八年位居全球第一。我们的政策就是说2019年出了一个政策就是说,2021年1月1日开始我们要正式实施这个评价。到时候就是说我们风电跟当地的火电同一个价格。势必要促使我们整机的销售价格要下降,那这个价格下降最主要的推动力,就是我们风电这个技术持续的进步,那近十年呢,由于技术的进步带来风机的成本下降,已经下降了30%,右边这张图是国家发改委能源中心发布的一个显示绿色区域是我们平价还是可以开发。
在平价时代有一个存量风机的后市场,后市场这个规模是非常之庞大,可以说它是一个蓝海市场,抢装潮都关注在装置产能后市场的规模非常大,我们风电的运维市场我们年均增长率在10%以上。2020年我们有11万台风机要出质保,到2023年我们运维的市场将突破200个亿这是非常大的市场,与此同时呢,我们由于国内整机产能的饱和,还有在评价的背景下,整机销售的利润,肯定会进一步压缩,我们整机企业也会把这个业务伸向多元化其中风电服务是一个非常重要的阵地。
总体的趋势呢,就是平价是推动风电机组利用效率更高,智能化程度更高。第二块是叶片运维的现状,在役叶片,我们根据叶片统计发现叶片在役风力发电机组大部件的占比非常高,数据显示占比超过40%,包括简单的磨损开裂整个折断失效,叶片生产成本占风机成本的20%,如果这个现场叶片它一旦失效,甚至折断,它的更换成本非常高,尤其早几年的叶片,我们现场的吊机成本非常高,我更换期间导致停机,电量损失也是非常惊人。
叶片失效原因有很多,其中50%来自于生产过程缺陷,很多缺陷。另外比如说长期赋役的疲劳性还有雨石雷击,甚至是鸟撞,我国风电产品受政策的影响是比较大的,这两年抢装潮我们叶片严重供不上,产量和质量之间如何把控平衡,这是鱼和熊掌不可兼得的过程。缺陷对赋役有影响一个是裂纹,一个是褶皱,一个是里面有异物。
据我们运达统计现场失效导致叶片失效主要的位置一般出现在比如叶根位置,那么还有最大弦长处,叶尖位置,前沿后沿表面等等。总结一下对于我们现在在风电场运行的叶片,它损伤的发展机理,还有损伤位置,损伤后如何定量的去评估处理,其实还需要很多研究,就说它的原因还不是特别清楚,初始损伤也很难分析,事后分析难度是挺大的。
我们这个叶片其实是朝着一个更长,更大更重的一个趋势发展,那其实对我们的一个材料工艺带来了非常大的挑战,一旦失效带来的更换成本很高,所以说我们对这个在役叶片实施提前预警,损坏的提前预警,实现防微杜渐非常有意义。提前预警可以统计初始的损伤,可以返补我们前端的设计,针对每一只叶片的统计,建立相关的健康档案,实时预测每一只叶片剩余的寿命。
目前在役叶片损失检测两种方式,一种是通过塔底木视的方法进行外观的检测,另一种是用吊兰的形式,把工作人员吊运到叶片上,手持超声波的方式,对叶片内部进行检测,目前第三方的运维公司越来越多,使用这个受持超声的方式,检测叶片的内部,很多失效原因有可能是内部一些裂纹分层。这个缺点就是说目视精度非常低,手持超声仪,如何实现叶片在役叶片智能检测其实是我们国家提倡的智慧运维非常重要的主张部分。
我们运达关于在叶片损伤检测做了一些非常详知的技术调研,我们技术当中可以分为两类,一类是在线的监测,一个是离线的检测,在线监测24小时实时对风电场结构健康的监测,有声发射,基于振动的,基于应变的。离线检测有很多我们现在市场上能看得到的机器视觉,就是无人机,还有机器人这种,还有用超声,超声我刚才说的手持超声其实,超声有很多种,X射线涡流法也可以做无声前侧,对我们风电不是很适用,红外是非常重要的发展方向,目前由于一方面红外的像素比较低,另一方面观测的深度还不够,红外只能检测到内部大概几毫米深度的一个结构。
除了是否连续的检测之外呢,我们还从不同维度的结构来进行分类。从零维到三维检测技术进行分类,振动是零维的因为是综合性的,你知道它损伤发生在哪里,一直到三维就是说我们表面和内部结构的健康,同时进行检测,我们最终目标是希望在线实时实现一个三维的表面内部的结构都能实时监测的技术,其实目前来说还是比较难实现。
我们分成两条技术路线,这是行业内的共识。一条是在线综合性的损伤监测,一个是离线三维的损伤检测。在线使用是在线监测系统是基于振动载荷传感器等等,我这个报告主要讲的是离线的检测,我们用的是一个基于叶片爬行机器人,然后结合了我们现在观察表面比较成熟的机器视觉和检测叶片复合材料内部结构目前最有效的相控阵超声两者结合。
下面简单介绍一下我们运达这个方案,我们对设备的研发看重安全性,效率第一安全第二,再考虑成本,我们设置多重安全的保障,为这个保障检测机器人的安全保障我们风机本底的安全,机器视觉加相控阵超声,还能够检测叶片内部尤其是我们大梁的结构内部,因为大梁一旦有问题,脱胶了产生裂纹了,叶片有折断的风险会造成重大的安全事故,机器人为载体,使它设备可以非常精准的一个控制,包括我们机器人本体的控制,然后超声探头的控制等等。这个离线的三维检测是定期检测,就像我们人体一样,我们每年都要去医院做一个体检,就像人一样,我们的风电叶片其实也是需要定期的去做一个详细的检测,这是非常有必要的。
我下面介绍一下我们这个设备的主要组成部分,第一个损伤探测系统,我们是用相控阵超声实现三维结构的损伤探测。
第二部分是运动控制系统,运动控制系统,超声探头的控制,结构本身的运动,我们机器人探头叶片复杂表面的柔性贴合和精准的控制。
第三部分是数据处理系统,我们是在机器人上面配备了无限wifi,实现远程的无线传输,另外是通过机器学习相关算法优选算法提取特征样本训练,自动识别这个表面和内部结构的这个损伤。
第四个安全保障系统,我们在机器人尾部设置拖曳电缆,保证稳定的运行。上面有三个指示灯分别代表不同的状态。
第五个是路径规划,我们实现机器人在叶片上实施一个自动的一个检测,全自动的一个检测,那么就需要现场对这个叶片的外形做一个激光三维的扫描和建模。
第六个是辅助系统,提高超声探测精度清洁叶片表面。这个平台的关键技术一个是吸盘对曲面的柔顺贴合,稳定的吸附在叶片上,我们的实现显示,一个吸盘吸在叶片上,机器人可以抵挡住20米/秒的阵风。第二个是我们超声探头怎么跟叶片表面实施一个柔顺的贴合技术,超声探头它也是一个固定的装置,也必须实施一个完全贴合才可以。
我们当然是安全第一效率第二再控制成本,下面是大概的一个尺寸。这个作业过程大概是这样的,首先机器人就位,就位以后首先进行大梁的定位,大梁边缘找出来,机器人自动规划路径,规划完通过两种技术对内外进行检测,然后对这个机器人最后进行收回。
那么我再介绍一下我们检测结果,像中间这个图是检测大梁,大梁位置有一个褶皱的区域,我们做了一个实验,粘胶的地方做人为的缺陷,用我们的设备可以非常简单的就是检查出来它非常明显的结果。
最后对比就是传统人工是用肉眼检测效率非常低容易误判,手持超声仪效率很低数据不连续,受影响非常多,我们机器人检测可以实现结构内部的一个连续性检测,而且精度非常高,可以达到毫米级的裂纹缺陷都可以查出来,现场手持超声受现场影响比较大,效率很多,50米长的叶片一套叶片我们只要大概4个小时到5个小时就可以检查完毕,这个是目前来说在业内是最快的速度。我的报告就到这里谢谢各位领导各位专家的聆听,有什么意见欢迎批评指正,谢谢大家。